Checking Encoder Feedback on Intelitek Robotic Arms

This article can apply to any robot that is operable using recent Windows-based ScorBase or RoboCell versions.
For example, an ER-4U, or discontinued robots like the ER-2U, or ER-4PC.
Following the steps in this article will allow an operator to verify if an encoder is providing feedback to the software.
This can be useful for troubleshooting when there's an issue, helping determine if an encoder is working as expected, or recognizing if it's giving erratic numbers.
Consider also checking if the home switches are working properly.
Enabling the Encoder Counts dialog bar
- Launch ScorBase/RoboCell
- Enable Encoder Counts
Navigate to View > Dialog Bars > Encoder Counts and click it.

- The Encoder Counts bar will appear at the bottom of the software window.
The values generally start at 0 after being homed, and can go into the negatives.

- Now, when the arm is moved, the values for each axis will increase or decrease along with that movement.
Note: If the values are erratic or jump drastically, that could point to interference, such as dust, inside the encoder housing blocking the optical signal.
Movement can be performed by hand, or if able, by using the Manual Movement window and guidance is offered below if needed.

Axis 4 & 5 work together for gripper pitch and roll, so these encoder counts will change at the same time.
Axis 1 = Base
Axis 2 = Shoulder
Axis 3 = Elbow
Axis 4 = Wrist Pitch
Axis 5 = Wrist Roll
Axis 6 = Gripper Open/Close (not pictured)
Axis 7 & 8 = Accessories/Peripherals
Moving the robotic arm by hand

Be careful as this process requires using your hands, and the open design of the robot allows for pinching of your fingers if care and consideration is not taken.
Done correctly, this is a safe and straight-forward process, but if there are safety concerns please consider wearing thick work gloves to avoid chance of injury.
If your robot is not mounted to a table or linear slidebase, please have a second set of hands available to hold the robot in place if necessary.
- With the software launched, On - Line and Control On press the E-STOP on the controller.
This prevents the software or a Teach Pendant from moving the robot, but continues to allow signals between controller and software, and keeps the motors de-energized so they are not using power to hold position.
- Carefully grab the robot as necessary to move the axis suspected of having an issue, and move it in a slow, consistent motion.
- Depending on the direction of movement, you should see the encoder count value for that axis increase or decrease.
If your encoder count values change, the encoder is providing feedback to the software.
Note: If the values are erratic or jump drastically, that could point to interference, such as dust, inside the encoder housing blocking the optical signal.
If your computer screen is not easily visible while doing this, a second set of eyes may be needed.
- If you now move the same axis in the opposite direction, the encoder count value should reverse back to the value it started at.
If the value goes into the negative, this does not necessarily indicate an issue as it is expected depending on direction of travel.
- Repeat as necessary.
Moving with Manual Movement window
- With the software launched, On -Line, Control On, you should be able to move the robot unless there's a technical issue, in which case you may need to move by hand.
- Click on the Manual Movement window so it's active.
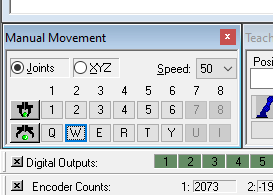
- Click an icon to move the desired axis in one direction, while watching the encoder counts bar to see the values change.
You can also use your keyboard:
1/Q moves Axis 1
2/W moves Axis 2, etc.
- If your encoder count values change, the encoder is providing feedback to the software.
Note: If the values are erratic or jump drastically, that could point to interference, such as dust, inside the encoder housing blocking the optical signal.
- If you now move the same axis in the opposite direction, the encoder count value should reverse back to the value it started at.
If the value goes into the negative, this does not necessarily indicate an issue as it is expected depending on direction of travel.
- Repeat as necessary.